Riveting the floors and the gussets
3h
July 17, 2023
Today was a bit of riveting and fabrication.
First, I riveted the hinges that are used to attach seat backs to the F-742 aft seat floors. The hinges are attached with the AN470AD4 rivets (except for a few holes that are shared with the ribs and use LP4-3). since the hinges are very soft and the floors are very thin, initially I avoided using the rivet gun and used DRDT-2 to set the rivets instead. It worked okay at best, a few rivets were "smeared" a bit, most likely due to a lack of rigidity in the tool.
Then I tried back riveting them with the back riveting block I have, and it worked much better. The block is just a piece of still with the hole for the squeezer dies. The die is used as a support for the factory rivet head.
I riveted the floors with the LP4-3 pull rivets.
I also riveted the F-656 gusset plates to the aft bulkheads. One flush rivet did not set well (the shop head was too small and skewed), so I replaced it. However, for some reason, the hole was enlarged, so I put an upsized NAS1241AD4 rivet. I think it was because the dimple was not formed very well (there was limited access to the hole, so when I dimpled it, I didn't hold the squeezer exactly perpendicular to the hole). The rivet still looks kind of ugly, but I don't think it is going anywhere.
Finally, I finished the forward fuselage gusset F-695. The third time is a charm!
The fourth hole from the right moved a little bit to the edge of the longeron, but it still has about 0.250" edge distance.
Drilling through the steel is still a bit of a challenge for me. Drilling the pilot #40 holes was fine, however, when I was enlarging them to the #30 size, I broke two drill bits. The issue is that the drill bit grabs the aluminum, cuts a "thread" in it, then thrusts into the steel and breaks. The technique that kind of worked for me was to use an air drill (which turns fast, so it cuts the hole through the aluminum before it gets to the steel) and feed it very slowly.
When I was drilling the holes for the external steps, I used a reamer to upsize to #30. Which was very hard on the reamer, but somehow it survived. This time I did not want to use the reamer to avoid drilling the holes at an angle (the drill bit seems to follow an existing hole better than the reamer).

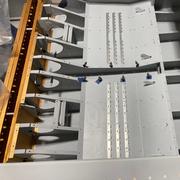



